yoootooobe embooods
As a new owner of an air compressor, you face knowing how to operate your new equipment correctly. This article…
As a new owner of an air compressor, you face knowing how to operate your new equipment correctly. This article will help answer the question that bugs every new air compressor owner.
How Does an Air Compressor Work?
An air compressor is a device that uses a motor or engine to store high-pressure air in a strong tank. It can use both an electric motor and a gas engine. High-pressure air contains a lot of energy, and when released it can be used to power various air tools.
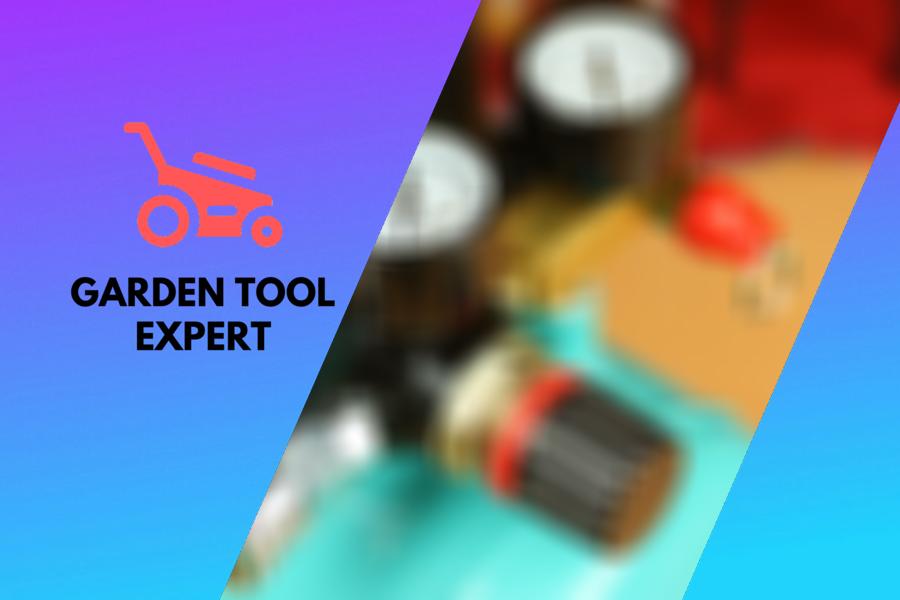
This blog will further explain what you can do with an air compressor, what the different types are, how to maintain a machine, and more.
What can you do with an Air Compressor?
Air compressors can be used for many different types of jobs:
- Tires: To fill all kinds of tires
- Painting: For air sprayers
- Air Tools: To power air tools like a nail gun
- Pneumatic tools: Gives a large amount of moderate-pressure air to power pneumatic tools, such as jackhammers
- Winterizing: To drain water from an irrigation system, or pipes so they can not freeze in the winter.
- Fill gas cylinders: Supply high-pressure clean air for filling gas cylinders
- Diving: Supplying air to submerged divers
- HPA: To fill high-pressure air tanks (HPA)
- Industry: There are all kinds of industrial processes where high-pressure air is used.
Air tools
Air compressors can be used for many different tasks. These tasks require an air tool:
- Nail guns: with this tool, you can drive nails into wood, walls, or any other material.
- Staple gun: These are used for driving heavy-duty wire staples into the wood and other materials.Grinders: This is used for grinding.
- Sanders: Make rough surfaces smooth.
- Drill: the air is used to rotate the drill head.
- Paint / Spray gun: The air is used to spray the paint on the subject. This makes the paint come out similar to a spray can.
Different methods to compress air
There are two effective methods of air compression. They are the Positive-displacement compressor and the Dynamic compressor. Both methods are subdivided into different categories, and the ways they work vary from each other.
● Positive Displacement
The positive-displacement compressor takes in air and mechanically decreases the space occupied by the air to increase pressure. Once the highest amount of pressure is reached, a port or valve opens, and the air is delivered into the outlet system from the compression chambers. The positive-displacement compressor is divided into three types which include:
– Rotary Screw Compressors
The rotary screw compressors have two inner screws that turn around in opposite directions while compressing air between them. They work by matching the two helical screws that, when turned, allow air into a chamber, whose volume is reduced as the screws turn. The rotary air compressor is one of the easiest to take care of. The engines are generally industrial-sized and are perfect for non-stop use.
– Piston-type
The piston-type air compressors use the rule of pumping air into an air chamber through the constant motion of pistons. One-way valves are used to guide air in and out of a chamber whose base is made up of a moving piston. When the piston is on its downstroke, it draws air into its chambers.
– Vane Compressors
The vane compressors are similar to rotary screw compressors, but in place of screws, vanes are installed on a rotor. These make use of a slotted rotor with various blade placements to allow air into a chamber and flatten the volume. The vane compressor gives a set volume of air at high pressures. They are relatively easy to use.
● Dynamic Compressor
Dynamic compressors apply the process of rotating impellers to move pressure to the air. The air is then controlled to generate pressure, and within the compressor, the kinetic energy is stored. The two major types of dynamic compressors are centrifugal and axial compressors.
– Centrifugal Compressor
Compared to other types of compressors, centrifugal compressors spin at higher speeds. They are designed for higher capacity because flow through the compressor is continuous. Centrifugal compressors can also be called radial compressors, and they work by conveying air into the middle of the compressor through a rotating impeller. This is then pushed forward by an outward force called the centrifugal.
– Axial Compressors
Axial compressors work with stationary bladed, which slows down airflow and, in turn, increases pressure. They are not so common and have restricted functionality. Aircraft engines and large air separation plants mostly make use of axial compressors.
Differences between a Compressor and an Air Pump
The words “compressor” and “air pump” are sometimes used to represent one another. As much as some similarities can be found, there is still a difference. An air compressor stores pressurized air in a tank, that then can be used to perform various tasks. An air pump does not store anything, it blows air from the pump directly out. The air pressure that comes out of an air pump is lower and the machine is much smaller.
Maintaining an Air Compressor
Like any other mechanical device, it is essential to perform routine maintenance:
● Pump oil level
If your compressor is oil-free, this part of the maintenance is not needed. But you must check the air compressor pump oil level for all other air compressors. When the level is low, it can destroy the pump.
- Step 1: Turn the machine off. Remove the mains cable if applicable.
- Step 2: Put the machine on a flat surface, and leave it there for 5 minutes.
- Step 3: Remove the oil fill cap
- Step 4: Check the oil level, and see how the oil looks. If it seems dirty, you should change the pump oil.
- Step 5: If needed, fill with oil. Make sure you do not overfill.
● Change the pump oil
If the oil in your pump is looking nasty or dirty, it needs to be replaced.
- Step 1: Turn the machine off. Remove the mains cable if applicable.
- Step 2: Make sure the oil is cooled. If you just used your machine, you have to give the oil some time to cool down.
- Step 3: Put the machine on a flat surface.
- Step 4: Remove the oil fill cap.
- Step 5: Put an oil container underneath the drain cap. You can also use an old bucket.
- Step 6: Remove the drain plug and let the oil fully drain.
- Step 7: Put the drain plug back. Make sure it is tightened sufficiently.
- Step 8: Fill with new oil. Wait a few minutes and recheck the level. If needed, add a little bit again.
● Clean or change the air filter
The air filter cleans the air that the engine uses. Over time it can get dirty or even clog.
- Step 1: Turn the machine off. Remove the mains cable if applicable.
- Step 2: Make sure the air compressor is cooled down.
- Step 3: Remove the filter cover. Normally there are a few screws that need to be unscrewed.
- Step 4: Get the air filter out.
- Step 5: Clean the air filter. You can use a vacuum if needed.
- Step 6: If the air filter looks bad, you should replace it.
- Step 7: Put the air filter back and reattach the cover.
● Other maintenance
To further prolong the air compressor’s lifespan, you should also check:
- Fuel tank: Ensure the compressor fuel tank is clean
- Shutoff system: Check the correct working of the air compressor shutoff system
- Nuts: Check the different nuts and bolts and make sure that they are all tight. The shaking of the air compressor may loosen some of them.
- Vibration: Check for more than usual vibrations or strange noises.
- Leaks: Check for oil and air leaks
- Safety release value: Check that the safety release valve is working correctly.
- Belts: Check the belts for wear and tear
- Pressure: Check the differential pressure in the compressed air filter
- Hose: Inspect the hose for damage and wear and tear.
- Temperature: Check and ensure that the operating temperature does not exceed a safe level
- Condensation: Drain the condensation from the air compressor tank
● How often should you check and maintain your Air Compressor
How often you should do maintenance on your air compressor differs significantly from your usage. If you use it daily, you have to check things more often than if you only use your machine sparsly.
– Before using your Air compressor:
- Drain the water from the air compressor tank
- Check for oil and air leaks
- Check for more than usual vibrations or strange noises
- Check the level of the Pump oil
– Monthly
- Check for loose bolts and nuts
- Check the safety release valve
- Check the air filter
- Belt check
- Check for air and oil leaks
– Yearly
- Change the oil in the pump
- If you have a gas air compressor, give the engine its yearly maintenance
Oil-free vs. Oiled Air Compressor
A dilemma faced by some people is trying to decide on the right kind of air compressor to get. One has to decide between an oil-less or oiled air compressor. Some tips to note when choosing either an oiled or oil-less Air Compressors include:
- Lubrication: Oiled compressors require frequent oiling while oil-less air compressors do not need any lubrication.
- Maintenance: Oil air compressors require more maintenance than oil-less ones. This is due to the needed oil change from time to time (although this also depends on the design of the air compressor and the number of times used).
- Long-lasting: Even though the oil-less air compressors are less expensive, and lighter, they do not last as long as well-maintained oiled air compressors.
CFM- What does it mean?
CFM means Cubic Feet per Minute and is the most common way to measure airflow. The CFM shows how much pressure a piece of equipment can provide, and the rate and volume by which the equipment tightens the air. External factors like heat, humidity, and wind influence the rate at which outside air enters the cylinder.
Frequently Asked Questions
● Do I have to refill my air compressor?
Yes, air compressors need to be refilled when the pressure level falls and the tank is almost empty. Air compressors have tanks that range from 1 to 6 gallons. A larger tank tends to contain more air and can deliver more air before the pressure level falls.
● Should you drain your air compressor?
Yes, you should drain your air compressor regularly. All air compressors will get water in their air tank due to the water in the air (humidity).
Bigger air compressors can contain a large amount of water (gallons) daily. On really big air compressors that are used constantly, it can be tens or hundreds of gallons of water daily. If you have a smaller compressor it will not be that much. But even a small amount is not ok for some jobs, like paint spraying. In that case, you have to drain the tank more often.
● How often should air compressors be drained?
It is recommended that the tank be drained once every couple of days. Also for certain jobs, like paint spraying, it is advisable to drain more often. The amount of water will depend greatly on how long you use your compressor and the humidity of the air. If you drain and see that there is a large amount of water, it is wise to drain it more often.
● Do air compressors last, and for how long?
Air compressors are generally highly durable tools. They can have a life span of 10 to 15 years, especially with regular maintenance.
Final Remarks
Air compressors work by changing power into potential energy stored in pressurized air. They are run by an engine that transforms electrical energy into kinetic energy. When this happens, the compressed air can then be used to run a variety of tools. Air compressors come in different shapes and sizes.
Air compressors are used for various tasks, and things like Nail guns, grinders, sanders, drills, staplers, and spray guns are all equipment that works perfectly with the air compressor. There are various types of air compressors, like positive displacement and dynamic compressors.
The positive displacement is sub-divided into three: piston type, rotary screw compressor, and vane compressor, while the dynamic compressor is made up of centrifugal and axial compressors. Each of these compressors has its way of working. The CFM is used to find out how much pressure a piece of equipment can provide and the rate and volume by which equipment constricts the air.
One should also carry out regular maintenance of the air compressors. For the efficient running of the air compressor, daily inspection is required. Things like checking if the oil needs to be changed, ensuring the operating temperature is at a safe level, drain condensation from receiver tanks, etc. Failure to do so can result in rust, wear, and tear of the compressor.
Oil-less air compressors are less expensive, light, and durable, but they do not last as long as oiled air compressors. In all, depending on the type of air compressor you choose, you must take time to study and understand how exactly it works.
Can you be more specific about the content of your article? After reading it, I still have some doubts. Hope you can help me.